El largo y complejo proceso para producir a mano el auto más potente y rápido del planeta
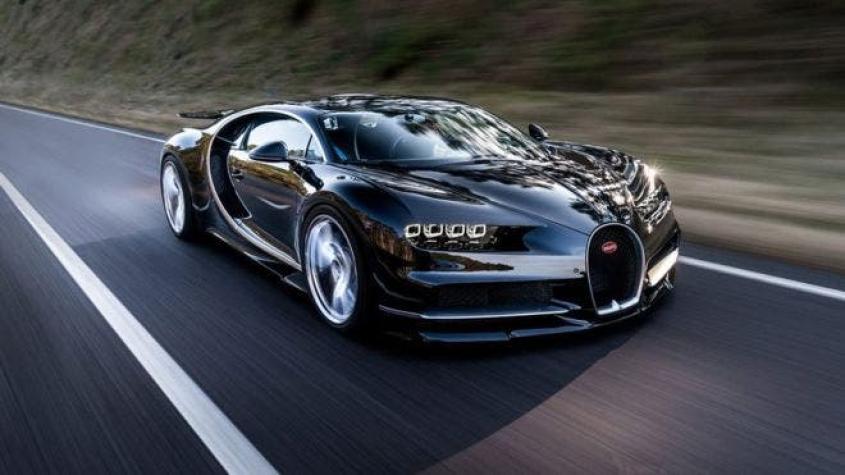
Más que un auto, es una bestia de 1.478 caballos de potencia que puede alcanzar los 467 km/h y es capaz de acelerar de 0 a 100 en un tiempo récord: 2,3 segundos.
El diseño del Bugatti Chiron, el nuevo superdeportivo que la marca francesa de automóviles de lujo presentó hace casi un año en el Salón de Ginebra -y cuyas primeras unidades entregará en el primer trimestre de este año- es tan exclusivo que fabricar cada uno de ellos cuesta seis meses y requiere la participación de 20 personas.
Su nombre hace honor al aclamado piloto de competición Luis Chiron y, según su fabricante, es el auto "más potente, rápido y lujoso jamás fabricado".
Chiron es 0,2 segundos más rápido y un 25% más potente que su antecesor, Veyron, que superó por primera vez en la historia la barrera de los 400 km/h y que llegó hasta los 431 con el modelo Super Sport, llevándose un récord Guinness en 2010.
La combinación de alta potencia con maniobrabilidad cotidiana fue, justamente, uno de los logros del Veyron, según dicen los expertos del sector.
"Comenzamos el desarrollo del Chiron como una mejora del Veyron, y terminamos con un auto de alto rendimiento completamente nuevo", le contó el ingeniero Dennis Rohlfs a la revista de automóviles estadounidense Car and Driver.
El nuevo deportivo de Bugatti cuesta tres veces más que un Porsche 918 Spyder, como el de esta imagen. |
Según le explicó a ese mismo medio Willi Netuschil, el jefe de ingeniería de Bugatti, no sólo ampliaron los turbocompresores al hacer este modelo, sino que desarrollaron un sistema "nunca antes probado en motores de gasolina para la carretera".
"En términos de tecnología, navegamos por aguas desconocidas", dijo el especialista.
El nuevo auto de Bugatti tiene cinco modos de conducción que el vehículo elige automáticamente, según la velocidad. Por ejemplo, el modo "Top Speed" sólo está reservado para circuitos deportivos y para su activación es necesaria una llave especial.
Esto para hacer frente a las preocupaciones de que puede ser un peligro en la vía pública.
En términos comparativos. el rango de competencia de Chiron incluye a los legendarios McLaren P1 y Ferrari LaFerrari -la actual generación de superdeportivos- y también a otros híbridos presentados en la feria de Ginebra, como el Apollo Arrow (de 1.000 caballos y 360 km/h) o el Zenvo TS1 (1.100 caballos y 400 km/h).
La nueva joya de Bugatti cuesta 2,4 millones de euros (unos US$2,6 millones), un precio equivalente a tres Porsche 918 Spyder, el superauto de 887 caballos que marcó una época y que ya no se fabrica (sólo hicieron 918 unidades).
En el caso de Chiron, el objetivo es hacer 500 unidades, aunque este año la empresa fabricará sólo 70. Es decir, es una oferta para un mercado minoritario, de lujo.
Ensamblaje a mano
El proceso es tremendamente minucioso y exhaustivo.
Un mes antes del inicio de la producción se ensambla el monocasco (autoportante) con los subchasis (la "cuna" del motor) y los paneles de carrocería para comprobar que todo encaja.
Después, comienza el largo procedimiento para ensamblar a mano las 1.800 piezas que componen el vehículo. Una verdadera obra de arte e ingeniería.
La fabricación de cada vehículo requiere 20 personas y 6 meses. |
Se trata de una factoría totalmente nueva que se edificó para la construcción del Bugatti Veyron y que cuenta con una superficie de más de 1.000 metros cuadrados con un suelo tan blanco y limpio que, según la compañía, "se puede comer caviar sobre él".Cada una de esas partes del vehículo tiene un número de identificación y cada elemento es enviado al taller de pintura de la fábrica.
En esta fábrica no hay robots ni líneas automatizadas. No existe cadena de montaje. Los equipos humanos se dividen en 12 estaciones en las que cada uno de ellos trabaja como si fuera "una parada en boxes de la Fórmula 1".
El suelo de la fábrica es tan limpio "que se puede comer caviar en él", dice la firma francesa. |
Todo el proceso se hace a mano. |
Diseño a medida
El proceso comienza con una reunión entre el cliente y el diseñador en la que definirán los detalles de la configuración del deportivo. Entonces, la empresa solicita suministros a sus proveedores y comienza a trabajar en el chasis.
Una de las primeras etapas del ensamblado comienza con el acondicionamiento.
El motor es, por supuesto, el corazón del auto y la pieza principal. Llega a Francia ya ensamblado desde la fábrica de Volkswagen en Salzgitter, Alemania, y pesa 628 kilos.
Tiene 16 cilindros y se une a mano, utilizando como única herramienta electrónica una llave dinamométrica para ajustarlo que avisa al operario de la cantidad de fuerza que debe aplicar.
No existe cadena de montaje. Los equipos se estructuran en 12 estaciones de producción. |
Cada cliente personaliza su auto y lo configura a su medida. |
Una vez terminado el ensamblaje del motor, se unen el subchasis trasero y el delantero (monocasco) en una de las operaciones clave.
Ambas piezas están conectadas por 14 tornillos de titanio de 34 gramos cada uno.
Otra parte importante son los radiadores y la refrigeración del motor. Para comprobar que no existen fugas, los operarios llena los circuitos de refrigeración, los drenan, y los vuelven a llenar durante ciclos.
Además, cada auto pasa por un banco de rodillos (el más potente del mundo, según Bugatti) para poner a prueba su rendimiento.
La parte del ensamblaje termina en el centro de tecnología, a 200 metros de la fábrica, donde se terminan de montar algunos revestimientos exteriores.
Solamente hay dos mujeres trabajando en esta fábrica. |
En cuanto al interior del automóvil, se necesitan tres días para completar su instalación.
La pintura del coche, el pulido de las diferentes capas (entre seis y ocho) y la inspección final, además de la corrección de las posibles imperfecciones, se puede demorar hasta tres semanas.
También hay que colocar la tapicería y otro tipo de detalles, como las iniciales del comprador en el reposacabezas.
Después, se hace una inspección visual en el túnel de luz de la fábrica que dura seis horas, donde cualquier mínimo desperfecto es detectadp y corregido.
En el túnel de luz no se escapa ningún detalle. |
Una vez finalizada la construcción, cada auto es sometido a lluvias torrenciales y huracanadas de diferentes intensidades durante 30 minutos para comprobar su resistencia. Esto se lleva a cabo en el túnel de pruebas.
Finalmente, cada modelo se probará en carretera a lo largo de unos 300 kilómetros, una prueba muy extrema a 250 km/h en la pista del aeropuerto de Colmar, en Francia.
Si la supera, el proceso habrá terminado. Sólo quedará reemplazar las llantas y el aceite, y estará listo para su entrega y su puesta en marcha definitiva.
Pero, de nuevo el cliente tendrá que esperar. Esta vez, unos nueve meses más para recibir las llaves de su nuevo auto.
Y no existe carretera pública en la que se puedan alcanzar la alta valeocidad de este Bugatti o la cantidad de espacio para llevar sus neumáticos al límite.
"Hay que recordar lo grande que es la distancia de frenado necesaria en esos niveles", advierte Netuschil.
Por eso, Chiron está limitado electrónicamente para no rebasar los 420 km/h. Una velocidad punta que, sin embargo, todavía no lograron superar sus competidores.
La prueba final: un paseo a toda velocidad por la pista de aterrizaje del aeropuerto. |